The focus of Industry 4.0 for manufacturers is on interconnectivity, automation, machine learning, and real-time data to build a sustainable, scalable enterprise.
Industry 4.0, in the manufacturing sector, is also referred to as IIoT or smart manufacturing. In today’s business environment, manufacturers need tools that help them streamline tasks, boost productivity and collaboration, and leverage data in real time.
Smart manufacturing marries physical production and operations with smart digital technology, machine learning, and big data to create a more holistic and better connected ecosystem for companies that focus on manufacturing and supply chain management.
While every organization is different, they all face a common challenge – the need for connectedness and access to real-time insights across processes, partners, products, and people.
According to Epicor, one of the best ways to understand the concept of smart manufacturing better is to think about how it could be applied to your business, or a business similar to your business.
Here are three use cases that can help you understand the value of Industry 4.0 in a manufacturing operation:
1. Supply chain management and optimization—Industry 4.0 solutions give businesses greater insight, control, and data visibility across their entire supply chain. By leveraging supply chain management capabilities, companies can deliver products and services to market faster, cheaper, and with better quality to gain an advantage over less-efficient competitors.
2. Predictive maintenance/analytics—Industry 4.0 solutions give manufacturers the ability to predict when potential problems are going to arise before they actually happen. Without IoT systems in place at your factory, preventive maintenance happens based on routine or time. In other words, it’s a manual task.
With IoT systems in place, preventive maintenance is much more automated and streamlined. Systems can sense when problems are arising or machinery needs to be fixed, and can empower you to solve potential issues before they become bigger problems.
Predictive analytics allow companies to not just ask reactive questions like “what has happened?” or “why did it happen?” but also proactive questions like “what is going to happen” and “what can we do to prevent it from happening?” These types of analytics can enable manufacturers to pivot from preventive maintenance to predictive maintenance.
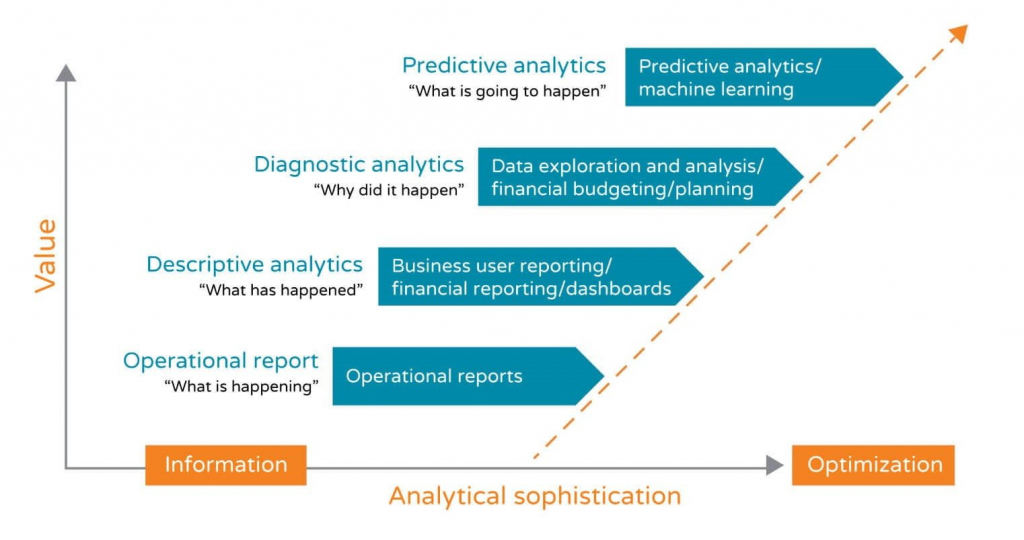
3. Asset tracking and optimization—Industry 4.0 solutions help manufacturers become more efficient with assets at each stage of the supply chain, allowing them to keep a better pulse on inventory, quality, and optimization opportunities relating to logistics. With IoT in place at a factory, employees can get better visibility into their assets worldwide.
Standard asset management tasks such as asset transfers, disposals, reclassifications, and adjustments can be streamlined and managed centrally and in real time.
Reviewing these use cases can help us imagine and start thinking about how smart manufacturing could be integrated into our organizations.
Sistema Plastics
Sistema Plastics was the proud winner of the Epicor 2018 ANZ Customer Excellence Award for Outstanding Technology and Innovation.
The award acknowledges not only the New Zealand manufacturer’s advanced automation around all aspects of its operations from manufacturing through warehousing to dispatch. It is also a testament to how well its separate systems for machine monitoring, ERP/MRP and Warehouse management are integrated to function together.
At Epicor Insights 2019 held in Las Vegas in April 2019, Sistema’s CTO, Greg Heeley shared the company’s journey into smart manufacturing.
For the near future, Sistema is committed to process improvements, using technologies such as machine learning for analytics and planning, to drive efficiency and quality advancements, especially for predictive maintenance.
And people are at the center of that journey. Heeley said: “What’s important is giving staff the tools to help them do their work better, and aligning their skills to the jobs.”
To make the smart transformation successful, he offered some key ingredients:
- A leadership that supports the transformation
- A development team excited and committed to be their best
- A support team that helps make the right outcomes possible
“The tech team needs to ensure it is meeting business needs, not just ‘playing’ with the latest gadgets and widgets. An investigative team made up of various backgrounds and disciplines help to make sure development is in the right direction.”
Epicor ERP was ‘lived’ in Sistema in November 2015. The result?
“Automation allows the same number of workers to be more productive and more efficient,” said Heeley. “Integrating all the systems together allows smoother and more seamless processes, with better feedback to the factory floor as a result of the streamlined production and information flow.”