The Internet of Medical Things promises to improve medical care, but manufacturers need to choose test strategies that pay off.
The advent of the Internet of Things (IoT) is driving transformation in healthcare. This evolution is commonly known as the Internet of Medical Things (IoMT).
Today, we can easily find medical devices that are connected, such as ultrasound imaging systems, glucose monitors, bedside monitors, pacemakers, hearing aids, and wearable health monitors.
With IoMT devices, non-critical patients can stay at home and be monitored through these devices to decrease hospital admissions and reduce costs. We will see the IoT greatly influencing all aspect of healthcare segment, from monitoring, to diagnostic, to surgery and patient care.
However, medical device manufacturers face unique challenges when incorporating IoT because the equipment is often used in mission-critical applications. Therefore, they must be extremely reliable and long lasting. To meet such exacting requirements, manufacturers want to implement reliable, efficient, and cost-effective manufacturing test strategies.
The importance of exacting tests
While the high quality of medical devices is inherent at the design stage, that quality is subject to variances and defects in manufacturing, assembly process variation; supply chain component deviation; test system repeatability and operator handling. Some defects may not be detected during manufacturing tests due to lack of coverage in the test system. Marginally-passed units may cause field failures during actual usage due to degraded performance.
Manufacturing tests are normally optimized to achieve low cost and fast test time to meet market cost expectations. Thus, devices may only be tested under certain minimum conditions deemed sufficient to meet industry standards.
For instance, in production testing of Bluetooth medical devices, only a very simple connection test is performed. However, intermittent connection issues may surface only later.
Consider that a defect that is detected during initial manufacturing phases may not cost a lot to fix. However, the cost increases exponentially if the detection occurs after production testing or in the field by end users.
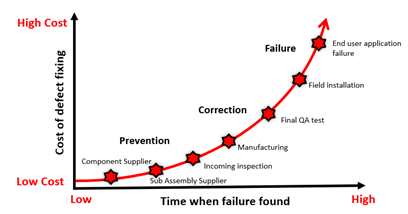
It is therefore important during the new product introduction (NPI) phase to ensure that the right test solutions are used. The caveat is that it may cost more to invest in more sophisticated tests and traine operators to execute the tests correctly. There are also annual maintenance and calibration costs. However, the potential savings from detecting failures early during manufacturing can eliminate indirect or hidden costs of field failure.
The hidden costs include warranty coverage, failure troubleshooting, handling of replacement units, loss of sales due to reputational damage, or even penalties arising from sale of defective products.
Three cases to consider
With the correct test strategies implemented in production, manufacturers can easily recoup the initial RF tester investment within the first year.
- Case study 1: Efficiencies through employing a versatile sophisticated testing setup
A medical device manufacturer with no previous experience with incorporating wireless connectivity could skip some tests during development because RF performance was guaranteed by the maker of one of the components. Instead of using standard design tests, the engineers were supplied with sophisticated albeit expensive test equipment that allowed them to perform extensive testing efficiently.
This same testing equipment was also used in the manufacturing tests, as it was cost-effective and simple enough for operator use. Therefore, the manufacturer was able to accelerate production and minimize correlation issues that frequently happened due to different test setups being used in design and manufacturing. - Case study 2: Pre-screening tests of wireless modules reduced manufacturing hiccups
A manufacturer faced yield issues with its high-end surgical machine, which included a wireless subsystem for remote control purposes. The wireless subsystem worked properly until failures started to show up. This became a big problem and impacted shipments, as the failures were discovered only after the complete machine was built and tested.
Much resources were spent on troubleshooting, repairing, and retesting. This caused inventory pileups and shipping errors. To fix this problem, the manufacturer acquired a simple and cost effective IoT signaling tester to do a pre-screening test of the wireless modules before they were installed into the wireless subsystem in the machine. Identifying defective modules before they were installed earned the manufacturer tremendous savings in test and repair time.
This eventually allowed the manufacturer to meet its daily output and yield targets. - Case study 3: Wireless tester helped simplify contract-manufacturing complexities
A contract manufacturer’s existing test solution was non-wireless and also cumbersome to maintain due to firmware management and complicated processes that could result in operator handling errors.
To improve production flexibility and eliminate operator handling errors, the firm switched to an IoT wireless tester that helped them to streamline test processes and easily switch between testing different product versions or brands, unlike the legacy test system. The wireless tester’s support of a wider range of wireless standards also enabled the firm to use the same test setup to test devices with different radio formats.
Such production flexibility is important for contract manufacturers, who cater to volume fluctuations from their customers.
Thorough IoMT testing is the key
Connected medical devices are on an exponential growth trajectory as they bring tremendous conveniences to patients, allow better healthcare delivery and lower healthcare costs.
The success of this megatrend will depend on the ability of medical device manufacturers to produce reliable and good quality connected medical device that will not fail prematurely in the field, through effective manufacturing tests that minimize the numbers of defective or marginal-quality devices that can fail in mission-critical end-user applications.