Automation is reducing the worldwide pool of skilled welders. However, when collaborative robots work hand-in-robotic-arm with humans, a win-win situation unfolds.
Without welders in the construction and manufacturing industries, the world would literally fall apart. Yet, this vocation has an uncertain future: a shortfall of 75,000 skilled welders is expected by the year 2026, reaching 150,000 thereafter, according to the Singapore Welding Society.
The work itself is dangerous in nature, requiring welders to be up close with extremely high temperatures, molten materials, and toxic fumes. The work can also be repetitive, involving long simple welds or hundreds of identical welds. Perhaps unsurprisingly, there are fewer young people going into welding and developing these skills. Like some other trades, the profession suffers from something of an image problem and the skill involved is not widely appreciated.
But what if welders could find better tools to make the conditions and workload of the job more satisfying? This is where robots come in.
Collaborative robotics in welding
According to the International Federation of Robotics, in 2021 welding applications represented almost 20% of all new robot installations and were mainly used in the automotive industry. However, with so much nuance and skill involved, replacing humans with automated welding machines is not a panacea. The industry needs a collaborative approach: one that can help augment welders’ productivity.
- A collaborative automation approach, where welders work alongside smaller robots, could help solve the skills shortage in welding.
- Human efforts can instead be focused on creating more complex and artistic metal work; jobs only human experts can do. This is where a robot collaborating with a skilled human welding workforce can add real value, while also creating safer working environments.
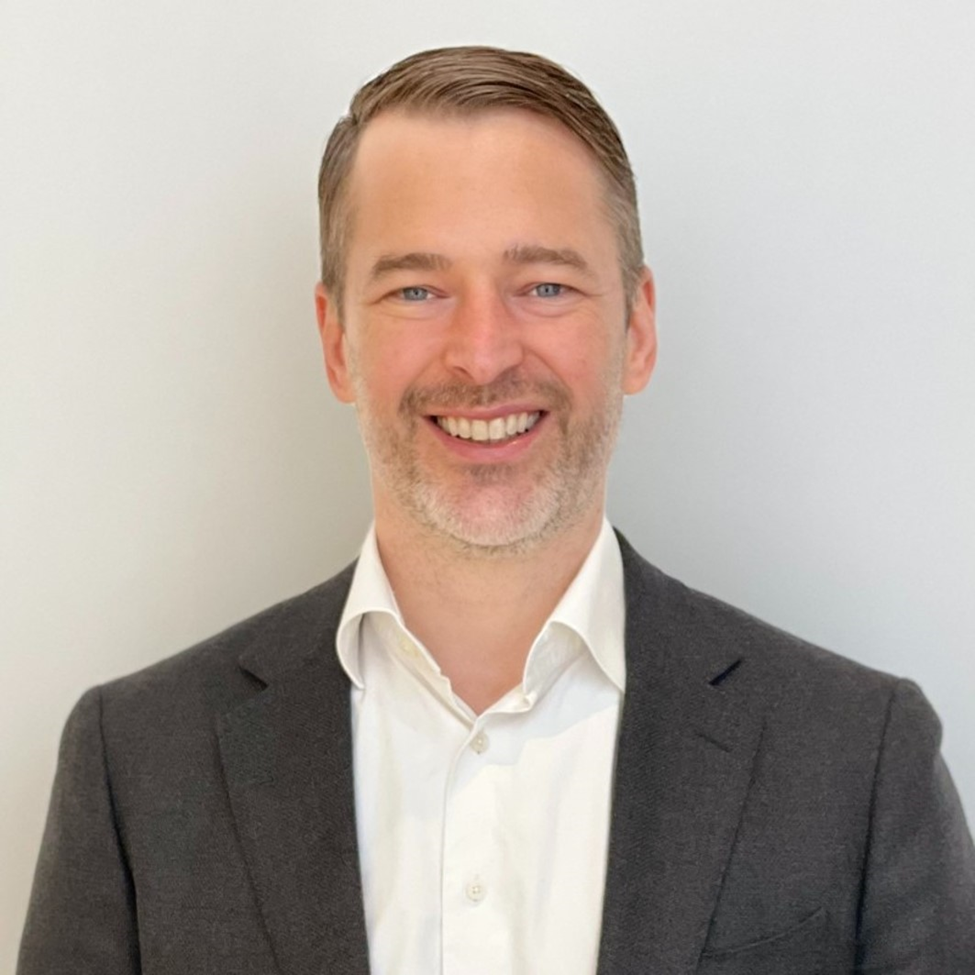
Yet, even with widely available technology in place, the use of collaborative automation for welding has only started to become more widespread in the last five years, following impressive innovation across a number of different welding firms.
The delayed adoption is partly a matter of awareness and partly due the perceptions of welders, who are skilled tradespeople. It is arguably harder to see the role of automation in a craft like welding, than in some other manufacturing activities such as lifting, packing, and dispensing. However, in reality, a cobot is just a tool, similar to a painter and his brush, or a baker and his mixer. Its main purpose is to complete repetitive tasks, rather than taking over the artistic element of the role.
With the demand for high mix and low volume metalwork rising, and a growing shortage of skilled workers, manufacturers are now under pressure to put collaborative welding at the forefront of evolving their sector.
Working hand-in-robotic-arm
Industry experts see arcwelding, metal inert gas and tungsten inert gas welding as the first focus for collaborative welding techniques, with plasma cutting, grinding and laser and spot welding fast following.
Not only can cobots empower welders to make more of their art — they are also improving job satisfaction for welders: removing the repetitive and dangerous tasks. Welders using cobots keep their creative freedom, and they are still needed to teach the cobot where to weld and what weld parameter ‘recipes’ to apply.
By easing the physical strain and monotony of certain welding work, cobots could help to tackle workforce shortages in the profession by keeping experienced welders working for longer and bringing in younger talent that is excited by the prospect of using collaborative technology.