With increasing digital transformation, industrial operations are collecting more data than they know what to do with: this needs to change
For many organizations, the value of data is going beyond merely informing leaders of economies of scale and paths of profitability. Real-time data helps ensure variables such as safety, reliable machinery, and sustainable operations are constantly monitored.
However, McKinsey Research is showing that data users surveyed spent up to 40% of their time searching for, validating, and preparing data for analysis.
Data only unlocks immense power when it is extracted, processed, delivered to the right people with the vision to put data to use and fit for purpose. Business leaders make better decisions after discovering useful insights on operational gaps and inefficiencies.
Data connectivity in industrial operations
It is common to encounter disparate data sources across plants, equipment assets and services these days. Consolidating these data sources is enough to pose challenges for businesses, let alone trying to make sense of data and deriving accurate insights.
Yet, industrial operations are becoming increasingly distributed and decentralized — engineering and project design teams involve individual expertise and inputs from the collective organization across offices, geographies and time-zones. Investments into IoT sensors, dashboard systems, and connectivity in multi-plant operations highlight that leaders are recognizing the value in real-time data across a wider operational footprint.
This value in real-time connectivity can be seen right here in Asia Pacific region. As the largest water operator in Malaysia, Perungusan Air Selangor (Water Management Selangor) distributes clean and safe treated water to households across Selangor, Kuala Lumpur, and Putrajaya. The facility’s Intelligent Command Centre (ICC) features enhanced operations observability through an end-to-end integration system for monitoring, analyzing, and modeling distribution systems in real time. This online system integrates real-time hydraulic data with hydraulic simulation models and statistical prediction tools.
Air Selangor is presently working on expanding this system with a future ‘Digital Twin’ feature, a virtual replica of the physical assets for real-time monitoring and predictions. The strategy is to improve data capture, asset reliability, and asset efficiency, that sets new standards for its quality of service.
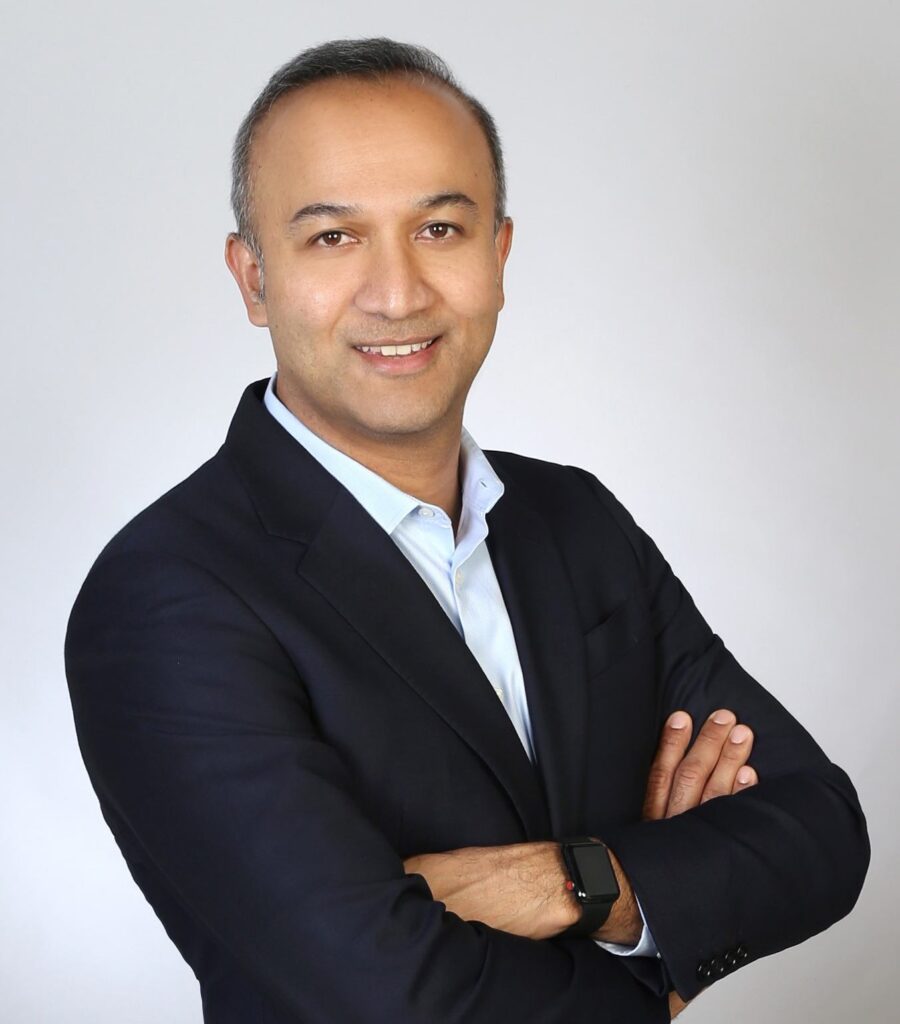
Don’t just collect data — connect it
While more organizations may have embarked on digital transformation projects, the reality is that there is no fixed endpoint in this journey. Breakthroughs in hardware and software are unlocking new pathways for growth. Organizations need to be well-positioned to seize these opportunities continually for growth through innovation and technology adoption.
As industrial enterprises transform digitally, they will be producing and capturing more operational data inputs than ever before. The vision of analyzing and aggregating data streams for new avenues of growth is well-intentioned. However, making sense of all these incoming inputs in a coherent and cohesive flow remains a realistic challenge.
To stay on course, enterprises need to integrate technologies to unify perspectives across work streams — thereby enabling better collaboration between teams. Data changes throughout an asset’s lifecycle (that is, in design, construction, handover, operations, and maintenance logs) — can present added complexities when so much provenance of a plant asset is in constant flux.
For Air Selangor, the objective of the Digital Twin of the operation plant is to empower project teams and engineers across various work streams and engineering disciplines to be able to refer to the same centralized virtual replica. They can then readily search for specific references such as parts, sections, or documents that are needed for plant asset monitoring and maintenance. This is one of many possible business outcomes when data streams are aggregated and analyzed properly.
Enterprises should therefore not just collect data, but connect the dots by leveraging integrated, edge-to-cloud data management solutions to improve asset reliability; reduce unplanned downtime; enhance collaboration; share timely and relevant information; and facilitate the development of customized products and services.
Addressing sustainability
On a broader scale, industries are now expected to account for environmentally responsible operations and predictive maintenance as part of plant operations. Sustainability goals demand a more definitive way to measure real-time carbon emissions and consumptions — aligning with the requirements stipulated by governing bodies.
Putting this into practice, enterprises can use connected data to bring to light problems and blind spots that may have been overlooked by employees working across different disciplines and project teams. This is critical in industrial plant operations, where no two plants are designed, or operationally identical.
Having precise data facilitates more accurate emissions reporting, production capacity, and asset reliability check-ups. All of this will serve a crucial role in industrial operations where data can deliver and measure more targeted impact and performance. For industrial enterprises to chart paths forward, collecting data alone is not enough. Harnessing the power in that data will help them unlock the next frontiers of growth.