The concept of modeling physical entities digitally for design simulation, testing and troubleshooting is a game changer for meeting climate deadlines
In the automotive industry, manufacturers are ramping up measures to run production sites on 100% renewable energies by 2039 and make sustainable factory planning a de facto decarbonization process going forward.
One well-known brand, Mercedes-Benz, is going even further. It is striving to create a scalable tool for the automotive manufacturing environment that can be used not just in its own facilities in Germany, but practically anywhere it builds cars around the world.
The strategy involved is Digital Energy Twin, which involves twinning a design’s energy needs for simulation in an identical, digitized model. The simulation technique makes early-phase design/energy testing, troubleshooting and solutioning faster, simpler, safer and more efficient in both brownfield and greenfield projects.
Based on behavioral models of buildings, technical equipment and energy generation, Mercedes-Benz’s Digital Energy Twin process was designed and tested at facilities in Sindelfingen, Germany.
Additionally, the firm’s digital energy twin solution features an open digital business platform that accelerates digital transformation, enabling customers and partners to jointly develop tailored products and solutions for various industries.
Therefore, this case study of combining the real world and the digital world to drive scalable, sustainable progress in industries is an exciting first step towards an integrated process for optimized building planning and operation/production in many other manufacturing and design sectors.
Using simulations for sustainable designs
Digital modeling technology connects inputs such as weather data, load-profile simulation, building asset selection and dimensioning to simulating a physical energy system. Various proposed planning scenarios for energy usage can be tested, verified and fine-tuned to achieve optimize desired outcomes including energy efficiency, associated cost savings, as well as emission reduction.
According to the firm’s Vice President of Production Planning, Arno van der Merwe: “The Digital Energy Twin is our answer to successfully visualize, analyze and sustainably optimize energy-efficient building processes. Through this innovative approach, we benefit from a better understanding of existing factory buildings and transform them into living smart buildings. Thanks to this transformative technology, we are maximizing their potential and setting forward-looking standards for energy-efficient and sustainable building use in Mercedes-Benz’s global production network.”
Partnering with a digital twin specialist has been a fundamental step in this endeavor. The firm chose Siemens — a firm it had already collaborated with since 2021 to achieve sustainable automotive production and ongoing digitalization of sustainable production methods. Siemens provides training and support, maintains and continuously develops the Digital Energy Twin for broad implementation across the Mercedes-Benz global production network. Its CEO of Smart Infrastructure and Member of the Managing Board, Matthias Rebellius, noted: “By accurately modeling operational and energy usage scenarios, the Digital Energy Twin enables faster and more transparent decision making in the early planning phases” to support industrial customers in achieving their sustainability and decarbonization goals.
Siemens provides training and support, maintains and continuously develops the Digital Energy Twin for broad implementation across the Mercedes-Benz global production network. Its CEO of Smart Infrastructure and Member of the Managing Board, Matthias Rebellius, noted: “By accurately modeling operational and energy usage scenarios, the Digital Energy Twin enables faster and more transparent decision making in the early planning phases” to support industrial customers in achieving their sustainability and decarbonization goals.
How a Mercedes-Benz factory looks like in digital-twin and physical appearances.
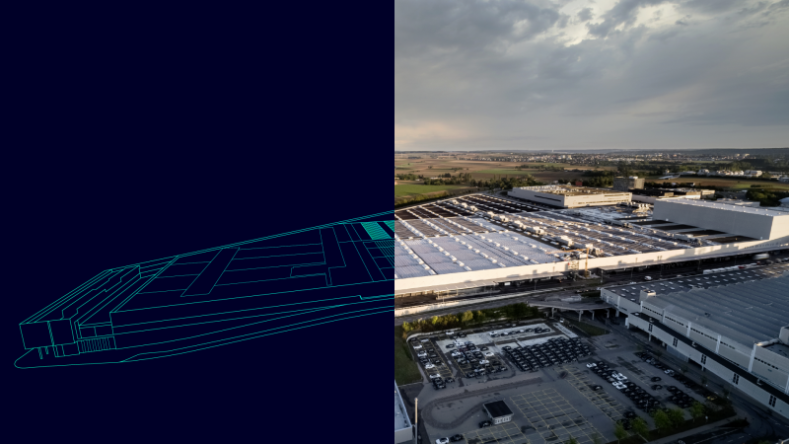