Businesses in ASEAN are required to move faster than ever to automate and digitalize entire value chains to tackle ongoing challenges of increasing costs, competition, and climate change.
With ASEAN’s digital economy poised to reach US$2 trillion by 2030, digital transformation for the region’s small- and medium-sized businesses (SMBs) is now more pressing than ever.
However, for that to happen in today’s digital economy would require cross-sector collaboration between the government and private sectors, while prioritizing sustainability.
How should SMBs in the region address the challenges to stay ahead of the competitive curve? DigiconAsia checks out some answers from Isabel Chong, Head of Digital Industries, ASEAN, Siemens.
With ASEAN’s digital economy poised to reach US$2 trillion by 2030, digital transformation for the region’s SMBs is now more pressing than ever, requiring public-private collaboration between government and industry sectors. How are these changes impacting SMBs across the region?
Isabel Chong (IC): SMBs are the backbone of Southeast Asia’s economy. The Asian Development Bank estimates that there are at least 71 million such enterprises in the region, making up 97% of businesses and employing 67% of the population. Digital transformation presents a huge opportunity for the region’s SMBs, and by extension the wider economy.
This is especially true against the current industrial backdrop of disrupted supply chains, cost pressures and demands for efficiency, faster innovation cycles, high-quality products, and greater flexibility. Above all, there is the pressing need for sustainability.
While digital transformation can appear daunting for organizations, especially SMBs that may lack financial or talent resources, not moving forward with it leads to the risk of being left behind by more forward-thinking competitors. It may also mean that companies miss out on the benefits and opportunities brought about by the digital economy.
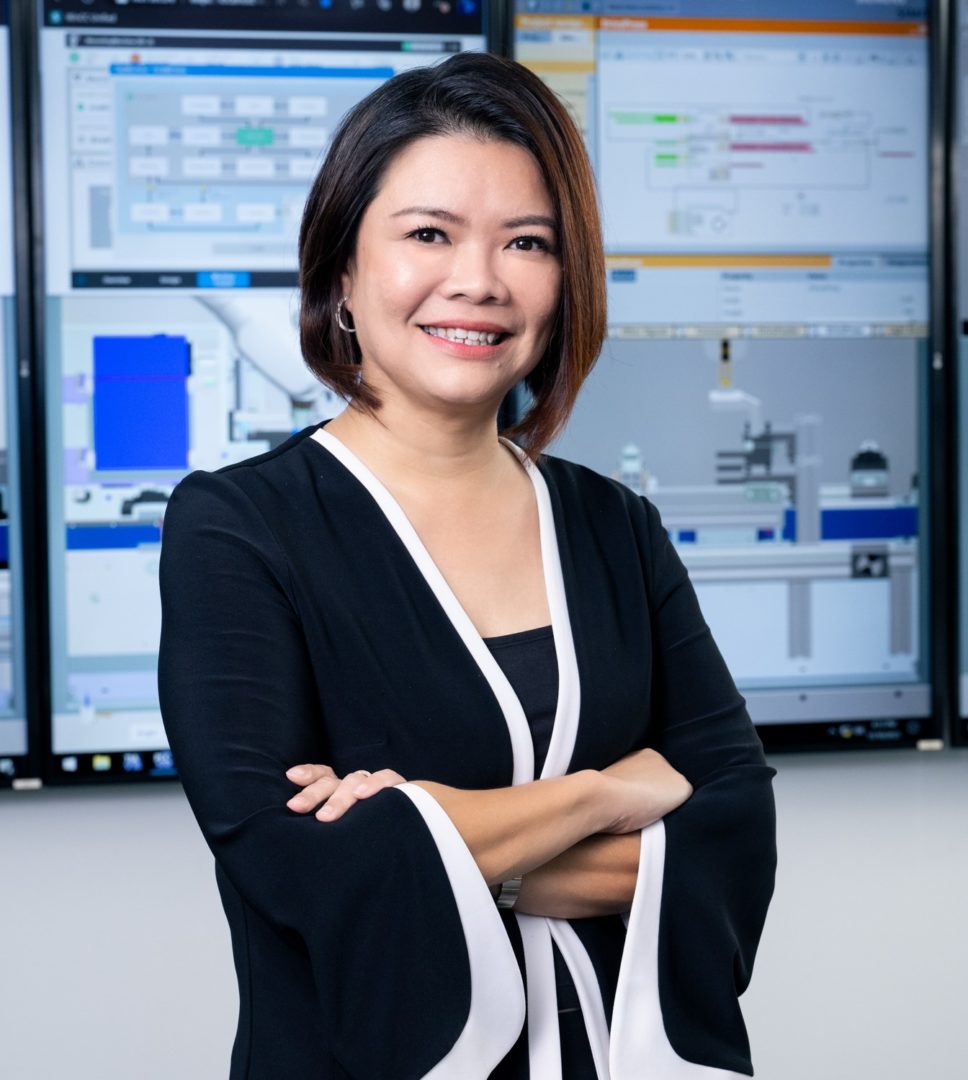
What can SMBs do to get ahead of the curve in the digital economy?
IC: SMBs must be able to transform quickly enough to remain competitive. In the digital economy, organizations that can adopt innovative and transformative strategies to increase their efficiency and flexibility, attract talent, strengthen product offerings, and lower costs are most likely to prosper.
The complexity of tomorrow’s smart connected products can be managed by businesses of all sizes and delivered today. SMBs which adopt personalized solutions that are easily adaptable to changing business conditions will be able to stay ahead of their competitors.
SMBs can now navigate digital transformation more easily than ever with an open, digital business platform that brings together customers, solutions, partners and developers in a curated environment to let them discover, exchange, inform, engage and co-create industry solutions – faster and at scale.
For instance, Siemens Xcelerator is a platform that supports companies of all sizes in their digital transformation. One of the tenets of the Siemens Xcelerator portfolio is its comprehensive digital twin. It creates closed-loop connections between the real and digital worlds with a digital thread across the value chain of product design, production and performance.
For SMBs, integrating domains provides a wealth of technological advantages from the ability to reduce the number of prototypes and removing bottlenecks to capturing real-time feedback in a closed loop environment. Just this alone can lower the cost of designing and manufacturing better products faster.
SMBs can also work with Siemens on upgrading their capabilities and developing new and improved products. As part of the program, SMBs in the manufacturing space can test-bed the end-to-end manufacturing process, to pilot projects, and to hone solutions for designing, manufacturing, implementation and monitoring. They would also receive consulting services and training by Siemens and its ecosystem partners.
Leveraging the new skills acquired, SMBs can upgrade their business operations through digitalization to optimize efficiency, improve innovation speed and product quality, while lowering costs. This initiative is part of Siemens’ wider commitment to supporting SMBs across Southeast Asia to explore, innovate, and pilot new solutions, and upgrade their capabilities.
How is Siemens’ Digital Industries initiative enabling sustainable digital transformation of SMBs across ASEAN? Please share some key examples of such digital transformation projects in the region.
IC: A great example is our partnership with Singapore’s leading modern indoor hydroponics farm, Artisan Green.
Singapore’s heavy dependence on food imports, which account for more than 90% of our food supply, exposes us to potential food security risks. These risks are exacerbated by factors such as population growth, urbanization, climate change, and unprecedented events like the COVID-19 pandemic. With that in mind, we need new ways of smart farming that integrate automation and digitalization, so as to produce more with less, and to produce locally.
Our partnership will leverage automation and digitalization, and a focus on plant science to advance sustainable farming operations at Artisan Green’s farm. We have created a Farm Management System that will enable Artisan Green to remotely access and monitor the farm operations, select the right cultivation program for each crop, plan and schedule demand, and optimize seeding and growing tasks.
In addition, with Artisan Green’s proprietary Precision Nutrient Injector, a chilled water-cooling system, and Siemens’ energy management software, Artisan Green can now effectively reduce the energy consumption of traditional indoor growing systems by half. As a result, Artisan Green’s new farm is projected to operate at only 15 kWh per kilogram of produce, exceeding the Singapore Food Agency’s Clean & Green standards.
The great thing is that this partnership will also contribute toward Singapore’s ’30 by 30′ goal, with the newly integrated farming operations enhancing crop quality and yield. It is expected to produce 25 tons of greens per month, which is estimated to generate a monthly supply of over 134,000 meals with leafy green vegetables.
This is a great example of how we can strengthen sustainable farming in Singapore through digitalization and automation. It is also an approach which can be rolled out in our neighboring countries to help mitigate the impacts of climate change on food security.
Another example is our partnership with Cocoa Teaching and Learning Industry (CTLI), a state-sponsored enterprise run by the Universitas Gadjah Mada in Batang, Java, Indonesia. UGM CTLI wanted to drive the Indonesian cocoa industry forward by providing farmers with training and access to technology, developing a better and more stable network, and establishing certification and quality standards that align with international markets. The key to achieving this – digitalization.
Siemens’ automation and digitalization technologies enable CTLI to oversee and control its factory in real-time from anywhere at any time. The factory is additionally equipped with the AI-enabled Siemens Process Monitoring Analytics software, so that its machines can learn and teach themselves how to produce the “Golden Batch” – where the roasting process is completed in the fastest time, most energy-efficient manner, and with the highest quality.
CTLI also relies on the Siemens Industrial IoT application suite, Insights Hub, to monitor its plantations. It is currently developing an app to predict the quality of cacao yields based on weather conditions. This way, CTLI will be able to optimize its cocoa production.
How can governments and industry leaders help to nurture the next generation of leaders in ASEAN’s industrial edge computing space?
IC: World leaders in developing and producing the most advanced technologies to improve lives and impact society should play our part in nurturing the next generation of talents for the industrial field, with our own initiatives as well as in collaboration with governments.
Here are a few examples of what Siemens has done in Singapore and Malaysia:
- In Singapore, we signed a Memorandum of Understanding with the Singapore Institute of Technology in 2022 to develop a new degree specialization in the Robotics Systems program. The degree specialization will deepen graduates’ knowledge and skills in Industry 4.0 technologies for the advanced manufacturing sector.
- We had also recently concluded the Siemens Industrial Edge Competition, which challenged tertiary students to develop practical mobile and web applications using Siemens Industrial Edge – an open and ready-to-use edge computing platform designed to unlock the full potential of machine and plant data. The idea is to challenge students to put what they have learned in books into practice, foster their growth as future engineers and provide a platform for students to showcase their abilities.
- In Malaysia, Siemens has established the Siemens Innovation and Resource Training Center (SIRTC) that provides upskill training for Industry 4.0. SIRTC has partnered with many government-linked companies/agencies and local universities, such as Malaysian Investment Development Authority (MIDA) and Malaysia Technical University Network (MTUN), to develop training programmes and learning modules.
We urge industry leaders to invest more in ASEAN talent development and encourage more collaboration between the public and private sectors, equipping the next generation with the necessary skill sets to continue to innovate in the industrial edge computing space.