How the region’s manufacturers can – and are – responding to Industry 4.0, pandemic woes, and supply chain disruptions.
Disruptions and uncertainty in the past year have underscored the role of manufacturers in delivering products critical to the continuity of countless industries around the world.
With the APAC region accounting for nearly 48.5% of the global manufacturing output, what opportunities can manufacturers expect and how can they transform supply chains to reap advantages beyond the next disruption?
Looking ahead, manufacturers must demonstrate their ability to pivot, experiment with new operating models, and redesign their supply chains should they want to bring operational efficiencies to scale.
According to EY, Industry 4.0 is already transforming how South-east Asia manufacturers leverage digital technologies such as advanced manufacturing methods, human-machine interaction, advanced analytics and intelligence to optimize productivity and further strengthen their position as “factories of the world”.
In the light of a recent study by Forrester Research that Aruba commissioned, DigiconAsia discussed the state of smart manufacturing in the region with Justin Chiah, Senior Director, Southeast Asia, Taiwan and Hong Kong (SEATH), Aruba.
How has the turbulence in manufacturing and supply chain impacted manufacturers? What are the sector’s current key priorities?
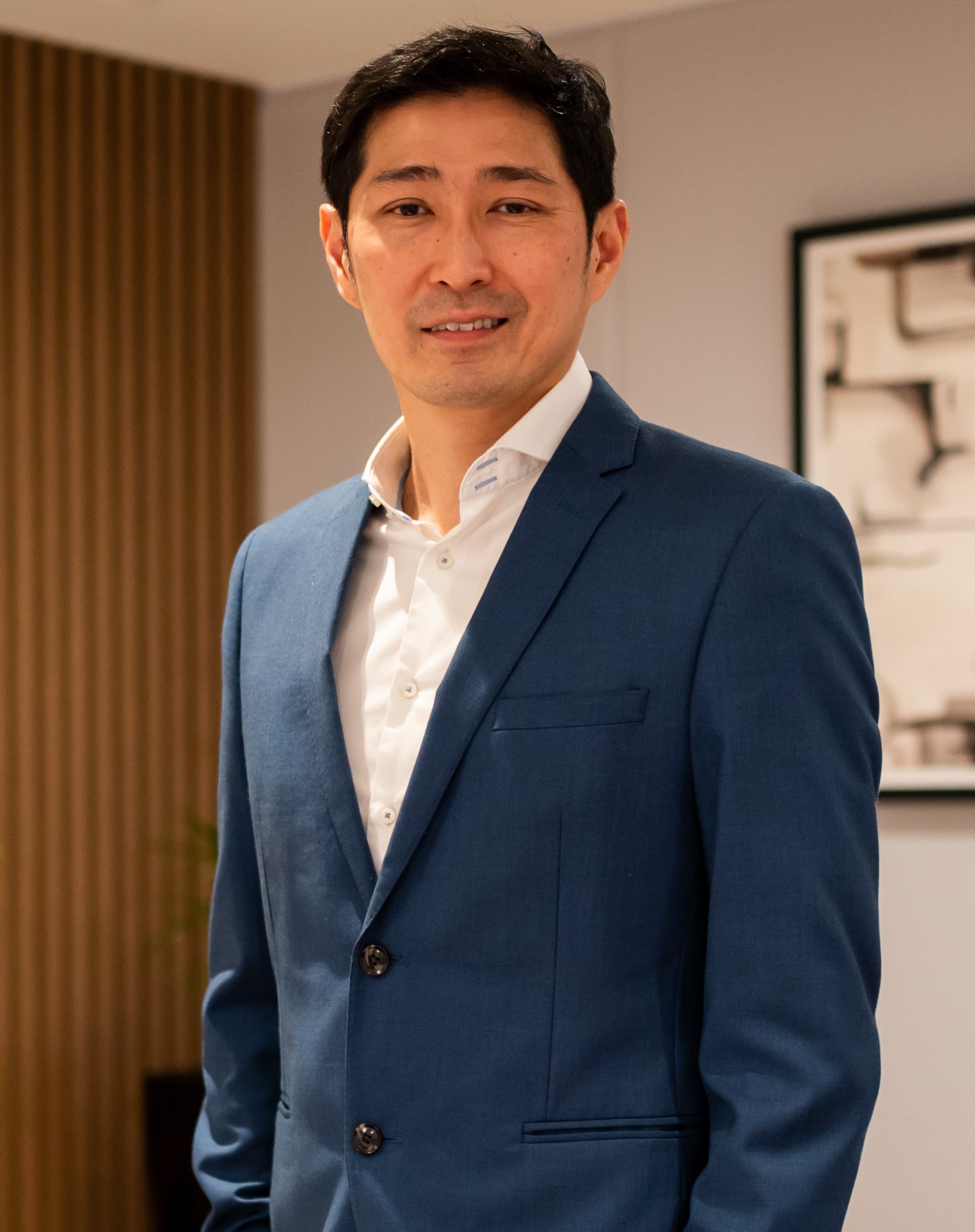
Taiwan and Hong Kong (SEATH), Aruba
Chiah: The turbulence in global supply chains brought about by the Covid-19 pandemic and the recent geopolitical uncertainties has underscored the need for global manufacturers to rethink and adapt their supply chains to cope with unforeseen international events.
Yet, in the middle of the turbulence, opportunities are emerging for regions such as South-east Asia (SEA) which is situated at the confluence of major trade routes. While international manufacturers may benefit from the region’s geographic, regulatory, economic, and demographic advantages, they must also address key gaps such as incorporating advanced digital capabilities into the supply chain and transforming the workforce.
As such, the need for high-tech manufacturing is critical now more than ever before. According to a commissioned study conducted by Forrester Consulting on behalf of Aruba, three in four manufacturers in Asia Pacific have been prioritizing innovation and automation for greater operational efficiency and resilience over the past year. Incorporating advanced digital capabilities into the supply chain is also critical to address shifts in the marketplace with agility.
48% of APAC manufacturers said the lack of cybersecurity features in legacy Internet of Things (IoT) devices is one of their top 5 challenges – why does this put manufacturers at risk?
Chiah: A comprehensive cybersecurity system is an indispensable aspect of IoT devices. Greater access to data empowered by IoT devices is bi-directional – if the network is able to access the devices to collect data, the rest of the network can be accessed from the IoT devices as well.
This poses a risk as without the proper cybersecurity measures such as network level dynamic segmentation or zero trust architecture, these IoT devices can become tremendous security risks that might ultimately undermine the organization’s competitive advantage, and customers’ trust.
The utilization of IoT devices to harvest data that provide valuable operational and business insights must therefore also be accompanied by an equally comprehensive cybersecurity system which prevents IoT devices from becoming a potential vector for malicious exploitation.
Beyond reaping the benefits of high-tech manufacturing such as convenience and cost-effectiveness, manufacturers should look towards leveraging tools such as cloud-managed networking and SD-WAN to alleviate data privacy and security concerns.
How are manufacturers realizing efficiency benefits from scalability and integrated network management?
Chiah: Manufacturers have to leverage next-generation smart networking solutions that are not only comprehensive, but easy to implement, maintain and scale, if they want to continue reaping the benefits and efficiency of high-tech manufacturing.
An integrated network approach in today’s manufacturing landscape is more often than not characterized by automated network intelligence, ease of implementation, as well as vastly improved network functionalities. Manufacturers that have successfully integrated such an approach into their operations enjoy a significant improvement in network performance, even as they continue to increase the number of IoT, edge, and automation devices to their infrastructure.
With legacy IoT devices in the past, this may have otherwise resulted in major network congestion. Intelligent networks on the other hand, are capable of dynamically adjusting device connections, to ensure mission critical components are never starved of network performance, while maintaining reasonable performance for the rest of the devices. Indoor network infrastructure is also just beginning to support precision location services, enabling accurate location data for connected devices.
Such data opens the door for a whole new wave of optimization, with the ability to track indoor equipment, automated or otherwise, providing much needed GPS accuracy and standardization for optimization algorithms. Corresponding improvements in resource management is also made possible, allowing companies to fully utilize what might have been previously idle resources.
How are global manufacturers moving to smart manufacturing with intelligent networking, and driving Industry 4.0 with IoT?
Chiah: Industry 4.0 is transforming the way global manufacturers operate in terms of producing and distributing their products. From cloud computing and analytics to artificial intelligence and machine learning, these are just some of the Industry 4.0 technologies that forward-looking manufacturers are moving to include across their operations.
With the accompanying high performance network connectivity alongside wide support capabilities for devices within their smart factory, Transcend, a global manufacturer and distributor of memory and multimedia products, now possesses real-time information reporting of equipment and production statuses which improve their business needs for collecting and analyzing high volumes of data. Beyond this, the adoption of high-tech manufacturing has also enabled its employees to work borderless – a crucial aspect of many operating environments today in a post-pandemic era.
Similarly, KEMET Corporation, another electronics-based company, has also leveraged intelligent networking solutions to rapidly deploy Wi-Fi access points (APs) across the globe. The replacement of legacy IoT solutions with an integrated IoT system in this case has enabled a drastic reduction in time needed for deployment of APs from days to just a matter of a few hours. With this, manufacturing defects and inventory bottlenecks that plague supply chains are also minimized, reducing associated financial costs.
Next-generation smart manufacturing tools enable manufacturers to future proof their infrastructure on top of ensuring resilience and scalability in their supply chains. The intuitiveness of these smart systems also ensures that the entire process from installation to usage, poses zero downtime for employees to relearn or adapt to business processes. The benefits of moving to smart manufacturing are immediate and will propagate the entire value chain.